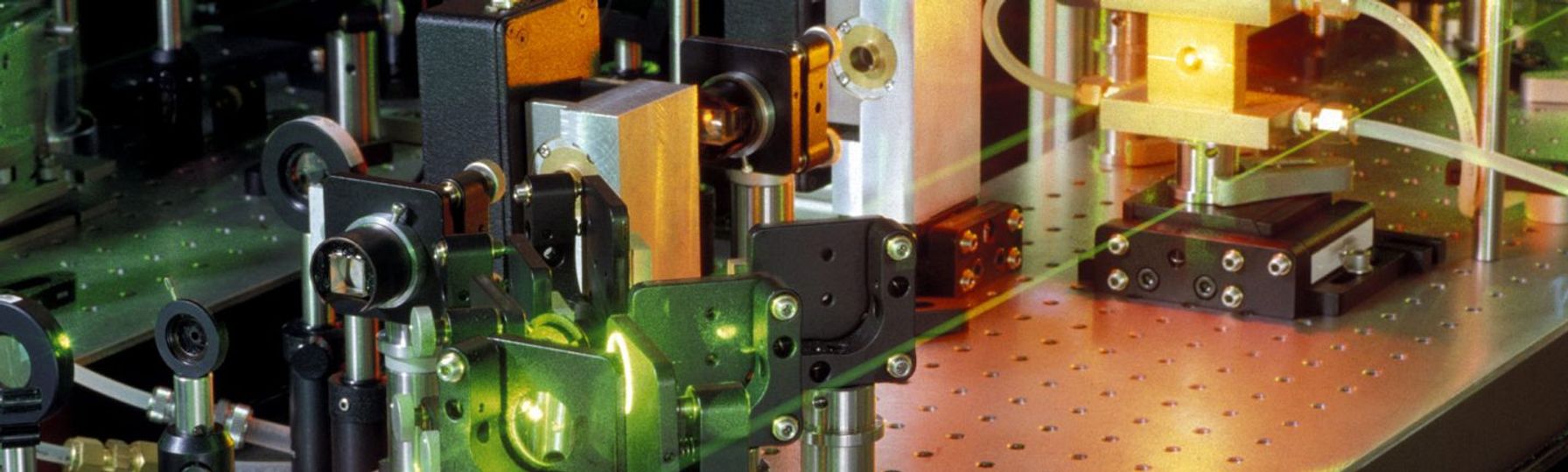
Health and Safety Programs, Assessment and Compliance
Laser Safety Solutions
Mitigate Risks Associated With Lasers
The use of Class 3B and Class 4 lasers is prevalent in materials processing, manufacturing, medicine, dentistry, education, academic and industrial research and development, telecommunications, entertainment and the military. A laser safety program is required to minimize the risks associated with these lasers.
The human and financial costs associated with laser accidents can be severe, including permanent eye damage and blindness, second- and third-degree burns, illnesses from laser-generated air contaminants, electrical shocks, electrocutions and facility fires. There are often multiple failures involved in a laser accident, including equipment related failures, uncontrolled and unanticipated beam path, lack of appropriate standard operating procedures, inappropriate laser eye protection and/or training gaps.
Laser Compliance Gap Assessments and Audits
TRC can assist your organization in navigating the complex laser regulatory environment by conducting a gap analysis or compliance audit.
OSHA does not have a specific regulation covering the use of lasers. However, OSHA requires employers to provide a workplace free from recognized hazards that could cause serious harm. OSHA references the American National Standards Institute (ANSI) Z136 series of laser safety standards as the basis for establishing an environment free from laser hazards. The primary ANSI standard that forms the basis for laser safety is Z136.1 American National Standard for Safe Use of Lasers. In addition, ANSI maintains a series of industry specific standards, including health care, educational institutions, research and development and manufacturing.
Laser Safety Program Development
TRC can develop a laser safety program that will minimize your health, safety and regulatory risks, including:
- Conducting laser hazard assessments and performing laser safety calculations, including maximum permissible exposure limit, nominal hazard zone, nominal ocular hazard distance and optical density
- Identifying required engineering, administrative and personal protective equipment control measures
- Evaluating and developing standard operating procedures for operation, alignment, maintenance and service
- Evaluating and developing a written laser safety program
- Conducting laser accident investigations and root cause analyses to identify corrective actions and lessons learned to prevent similar accidents from occurring
- Developing customized laser safety training
- Reviewing laser facility designs
TRC Laser Safety Experience
TRC’s laser safety services are managed by a Certified Laser Safety Officer (CLSO) with over 20 years of laser safety experience.
Looking for effective solutions to your problems?
Turn to the experts at TRC.